User:Nsilver
murmurmurmur welcome
Contents
Links
Fusing and Bonding
Making by adding | First brainstorm additive processes
- 3D printing
- clay, paper mâché, soldering
- Blending, lasercutter, gluegun
- 3D printer
- Knitting
- Embroidery
- Claying
- Melting
- Smelting
- Welding
- Soldering
- Stitching
- Paper mâché
- Taping
- Brick laying/mortar
- Lego/Knex etc.
- Cooking
- Stapling
- (new) kintsugi
- Paperclip
Projects development
At first I was thinking too much about product and too little about material and experimentation below is what I wrote and made then:
Lampshade (metal/paper Mâché, a historical example?) Research Lampshade DIY instructions Paper Maché lamp This was the first hit on google images when typing 'Paper Maché lamp' It is pretty common and easy to make your own DIY 'Paper Maché lamp, I want this lamp to have something different and unique. some photos That's why I want to play with the light coming from the lamp and add in colours, or reflections and maybe motion to the lampshade. [1]
Candle-wax sculpture
After receiving that feedback I wanted to just go and try. So I made this sculpture out of clay, wire, wood. It is fused by candle wax, I like the organic aesthetic it has. Jon did not seem to like it as much, I however could imagine a whole forrest made out of wire and candle wax, this could be used in an stop-motion film for example (thus also linking back to animation)
Tie-wraps structure
The tie-wrap construction is something that is strong yet very agile when it comes to moving and bending. It could be interesting to make an moving piece out of this. I can imagine a breathing statue if you will. The fact that it is woven makes it a historical example. I started on this however have not finished it INSERT PICTURE.
3D Printing in school
I have been wanting to explore the 3D printer for a while and this practise gave me a chance to do so.
On the right is the first model I tried to print, which did not come out as successful that was partly due to the kind of impossible mesh I made in this initial model. Below that is my first successful print. The model of which is shown on the left. I tried to make a structure which had a solid base and went up from there. So it would be easier for the printer to understand. It worked which was pretty exciting for me. I also liked to make it geometrical because this is just something I tend to do. Create order and shape things accordingly. Even in the initial model there is order, more organic but still there is order. Plus this geometrical precision is hard to achieve by hand but easy to achieve in the computer. One of the advantages of 3D printing.
I then pressed my printed tower into clay to make a mold as seen on the right.
Then i filled my mold with hot-glue to make a print. This did not turn out very successful, which can be seen here. INSERT PICTURE
I then wanted to test the limits of the machine by printing a crane as suggested by Jon. To see how the printer would handle something that is not very predictable. The overhang turned out quite nice and is something I could have explored further. This would be an example of a material pushed to the limit, but it can of course be pushed so much further. I should have explored this further, but I did not get the chance.
In the first lesson at Unfold Claire told me it would be useful to try out some of my design at the school 3D printer, which is what I did. These three trails for the workshop at Unfold. Besides a trail this is also my comparative example. Plastic vs. Clay, in clay you have many limitations you do not have in plastic. For example in plastic you van print over 45 degrees, which is not possible with clay since it will just tumble down. Also, plastic dries almost instantly and clay takes a week. However you can also use the ceramics you print in your oven and microwave. This would not be a very good idea with the plastic, seeing it would just melt. The ceramics also is more tactile and pleasing to the touch, this is of course a personal preference. The ceramics also seems to take less time to print since it prints thicker layers than the plastic. Plastic is then in turn not breakable and ceramics is. It really depends on what you are making, but for dishes pots and such the ceramics printer is my favourite. For designing things trails and integrate stuff the plastic will be a better candidate.
Something I wanted to explore was salt ceramics, however when me and Colin went to the printing workshop Dries told us that he didn't want salt in his oven because it gave of poison fumes. We made it a shared example by all accepting an fixed diameter for the lower (10cm) and upper ring (7cm), so that the cups should be able to stack.
| a video edited by Colin of our ceramic pots being printed at Unfold studio
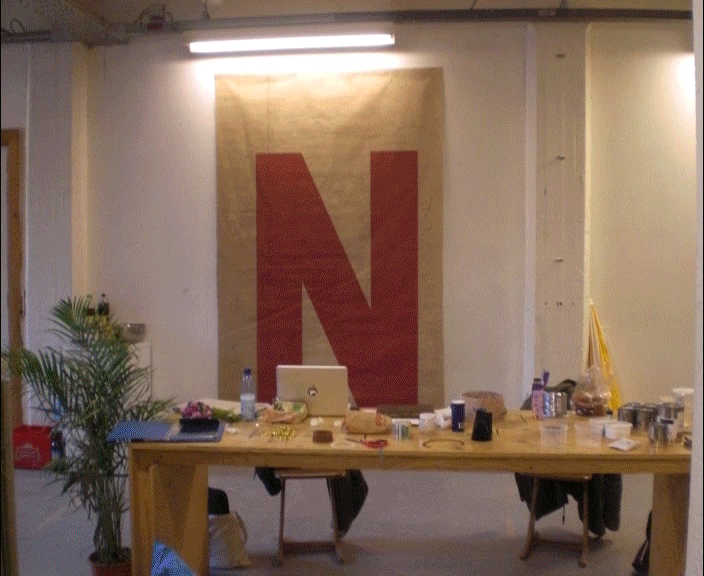
to do upload finished results
Ceramics station:
This is an example of a new skill
to do explain the difference between printing a pot and moddeling a pot on the turntable and describe the difference in experience and end result One clear difference I can already name is that with the printer you always get these layers, the hand-made pots are so much more smooth.
Things I would have liked to have done:
- continue to experiment with the 3d printer.
- breathing structure out of tiewraps, which I started as shown above but which is far from done.
Deliverables
- A historical example
- A comparative example
- An example of a new skill
- An example of a material pushed to the limit
- A shared example